Frequently Asked Questions (FAQs)
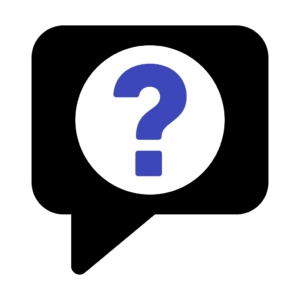
GENERAL TENSION CONTROL QUESTIONS & ANSWERS
Why tension control? How do I know when I need tension control on a machine?
If your manufacturing process involves –
• Printing on material that comes off a roll (ie. not • sheet-fed)
• Coating
• Laminating
• Extruding
• Slitting
• Rewinding, unwinding, or processing of any continuous web, ribbon or filament of any material
then accurate tension control can save you money.
Tension control allows manufacturers to dramatically reduce process deviations and inconsistencies which have negative effects on product quality, product rolls and sheets.
Typical tension related problems include –
Web breaks
Wrap-ups
Registration problems (colors misaligned)
Web deformation due to stretching or wrinkling of laminated substrate
Coating thickness variations
Unwind or rewind core crushing
Hard rolls or soft rolls
Telescoping rolls
All of these problems lead to excessive waste and low productivity.
By reducing material waste and allowing a process to run at higher speeds with consistent quality output, an effective web tension control system will not only improve a machines bottom line performance but will pay for itself in as little as a few weeks.
Complete this form to tell us about your application and we’ll recommend the right equipment configuration for you.
Where on my machine would I use DFE tension controls?
Dover’s tension control products are designed to be integrated smoothly into your machine’s structure wherever your application demands them–the unwind zone, rewind zone, intermediate zone, or any combination of these. Reliable, easy-to-install components that are also simple to use are the hallmark of a complete DFE tension control system.
— image —
Dover’s application specialists will help custom-tailor a tension control package to suit your exact needs. Working together, tension transducers, controllers, indicators, brakes, clutches and drives result in a level of process control previously unattainable. With an automated control system you will no longer need to monitor continually and re-adjust tension throughout your operation. Dover controls do it all for you. This saves you manpower, cuts downtime, and improves the consistency and quality of your finished product.
The Product’s section of our web site highlights major features and benefits of each of our standard products. Please inquire if there does not appear to be a product to fit your application. DFE delivers tension solutions for almost any continuous process machine.
Open Loop vs Closed Loop Tension Control
SteadyWeb 6™ Tension Controller or EasyWeb™ Torque Controller, which is right for me?
The SteadyWeb™ 6 Tension Controller is a closed-loop automatic tension controller with multiple capabilities to accurately control the tension of any material in any web fed process. To function, the SteadyWeb™6 controller requires a feedback signal from tension transducers mounted in the web path.
The EasyWeb™ Torque Controller is an open-loop controller used to adjust the torque applied to a roll of material as it is wound/unwound at the beginning or end of a process. While the tension of the material is affected by the torque adjustment, the EasyWeb™ is not a tension controller. To be a tension controller the EasyWeb™ would need some means of measuring tension. It’s missing the direct tension measurement as feedback.
How they work –
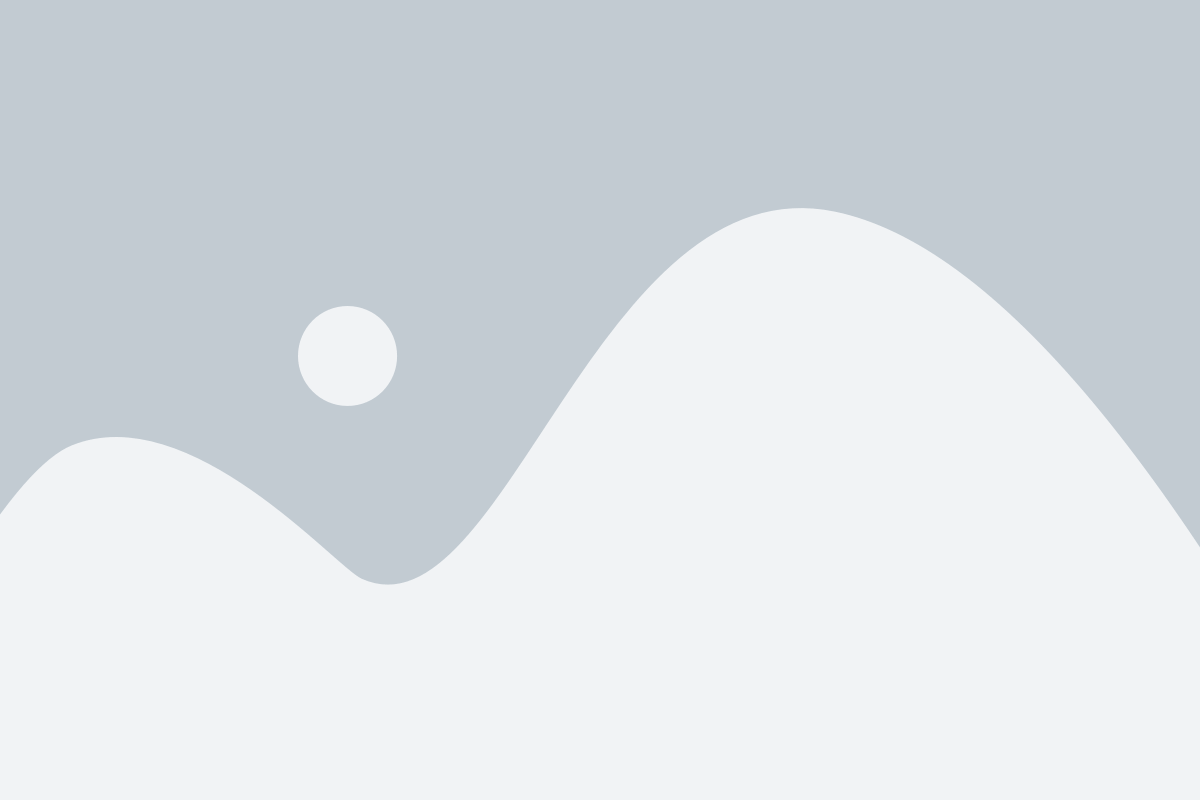
The SteadyWeb™ 6 Tension Controller has multiple capabilities for control. It can be used as an unwind controller, a rewind controller, or as an intermediate zone controller. The basic unwind/rewind control format would be to use the feedback from the tension transducers mounted in the web path to monitor the tension applied to the web material and automatically adjust the output to the brake or drive to maintain the material tension at the operator-selected set point. This is the same control scheme used by the cruise control of your automobile, you set the desired speed and the control system adjusts the output to maintain the speed at the desired point. The automatic control function of the SteadyWeb™ 6 is based on motor speed or brake/clutch torque to maintain the material tension.
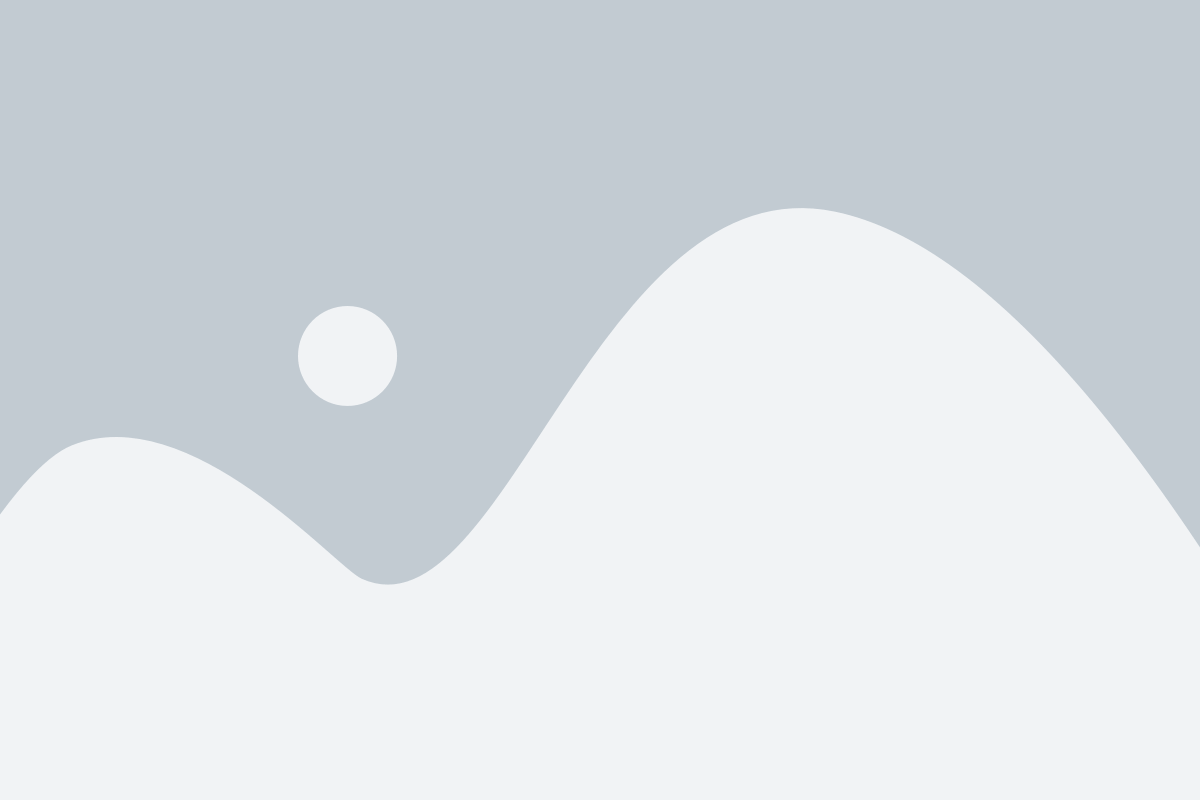
In addition to the basic closed-loop transducer feedback system mode, the SteadyWeb™ 6 can be set to operate in a speed-follow tension trim mode. In this mode the controller receives a line speed signal from the process and the motor follows this speed. The tension transducers (load cells) provide a feedback signal to the controller and it adjusts (trims) the speed signal based on the tension feedback so that tension always remains at the operator selected set point. This mode of operation is used in an intermediate nip application or in a surface rewind application.
A variation of this is the speed-follow diameter compensated tension trim mode. In this instance the controller is used in a center driven unwind or rewind application. The controller is provided with a line speed signal that is trimmed by the roll diameter (can be a measured or calculated diameter) that modifies the speed of the roll as the roll changes in diameter, and the transducer feedback is used to trim this modified speed signal to maintain precise tension in the material. In addition to these control modalities the controller can also provide a tapered tension function for rewinding materials. In a driven application for unwind, rewind, or intermediate use the controller functions by adjusting the speed of the motor to maintain the desired tension in the web.
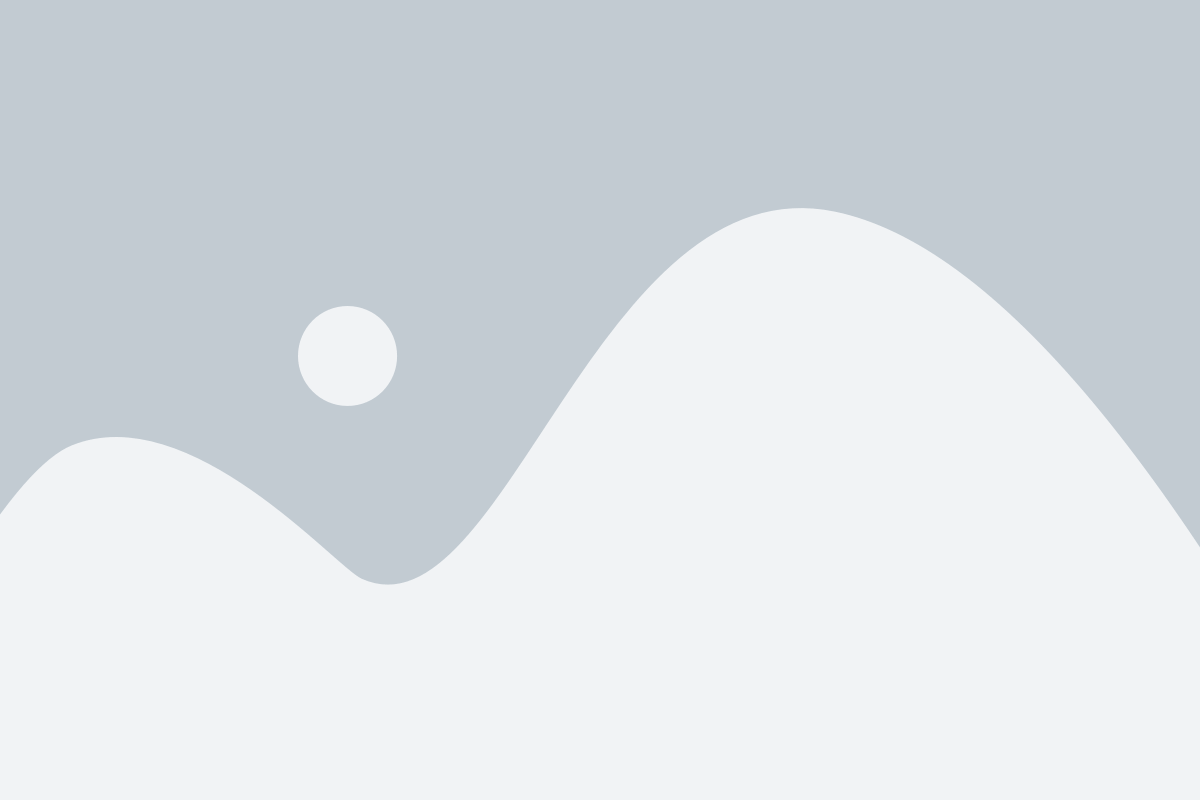
The EasyWeb™ Torque Controller functions based on the speed of the material passing through the process and the diameter of the roll being controlled. The line speed is used as a basis for the controller to provide the torque desired to operate the brake, clutch, or drive being used. The controller takes the line speed signal (DC Volts or encoder pulses) and a roll signal (can be a roll speed signal or a measured roll diameter) and calculates an output to set the torque of the controlled device. In the case of a calculated diameter the controller calculates the diameter of the roll based on the line and roll speed signals received. If a direct measurement, the controller adjusts the torque based on this diameter. The controller provides a decreasing torque signal for an unwind and an increasing torque signal for a rewind.
— insert image — EasyWeb simulation drawing
While these torque outputs do create tension in the material the control is not and can not be based on material tension as there is no feedback (tension transducers) to create a closed-loop control system. The EasyWeb™ can provide a tapered output for rewind applications similar to the SteadyWeb™ 6 but again it is a calculated taper and torque with no means of registering web tension.
The tension meter graphic in the above illustration is a calculated estimation only. This is taken from a screenshot of a simulation we run to demonstrate the principle of the EasyWeb™ Torque controller.
Controller Selection
The choice as to which controller to use in a given application is dependent on individual desires, criticality of control, and in some cases simply cost. It is safe to say that the SteadyWeb™ 6 is the best choice in almost all applications due to the simple fact that it is a closed-loop controller thus providing precise control and displayed results. However in the case where there is no space for tension transducers the EasyWeb™ is the best alternative.
For the price-sensitive customer, the EasyWeb™ will be somewhat less expensive to add due to the simple elimination of tension transducers and cables. Overall, if accuracy is desired it is always best to select the closed-loop option. However, if space for transducers is not available then the EasyWeb™ open-loop controller is an option that will provide dependable torque-based web control.
Don’t hesitate to contact us with questions or for a free analysis of your application.
What about tension controllers and data acquisition for tracking tension changes over time?
Customer Question: The label industry is very sensitive to curl and we are finding that controlling web tension on narrow web printing presses is very important. I work with customers using our flexible packaging and labels and am interested in learning how your web tension systems work and how we might be able to use a data acquisition system to collect web tension data over time.
Answer: DFE manufactures components for monitoring and controlling tension in any type of application. For a useful primer on web tension control and PID controllers see the article Tension Control 101.
Basically, DFE tension controllers come in three different output versions to correspond to the tensioning mechanism being used by the customer. The controllers can produce a pneumatic output (P version) for clutches and brakes, a low voltage 0-10 VDC output (D version) typically for motor drives or high voltage (V version) 0-24, 0-45, or 0-90 VDC outputs for eddy current or magnetic particle clutches or brakes.
For those applications requiring an interface to motor drives, our controllers can be used in a follower mode, where the control output follows the machine’s speed. Our newer controllers can also compensate for roll diameter changes when used on an unwind or rewind — e.g. the SteadyWeb™ controller. Line follower mode with diameter compensation is especially useful on machines with high accelerations.
All DFE electronics, whether they are closed-loop controllers or display indicators, produce a 0-10 VDC signal which represents measured tension over the calibrated range (for example 10 VDC = 250 lbs of tension). This tension signal can be brought into a data acquisition card for logging over a period of time. We can supply an off-the-shelf generic data acquisition card for this purpose, or recommend a brand-name card to you, and assist with setup for acquiring useful tension data.
If desired, a second channel of the data acquisition card can be used to bring machine speed in. Software normally used with these cards can be configured to show actual line speed and tension. This provides the capability to observe whether tension upsets occur when the machine’s speed changes, for example.
Some DFE tension controllers and electronics devices have RS232 and RS485 interface options. This allows a laptop computer to receive the data from the controllers and display it, using the serial port already present on most laptops. This may be the least expensive way to get tension information into a computer for analysis.
Select DFE controllers, indicators and amplifiers provide EtherNet/IP™ connectivity designed for use with supporting PLCs.*
If you have specific questions about how any of our components work, please email sales@dfe.com or call one of our Application Engineers at (603) 332-6150 to discuss your application. We can recommend which components are appropriate to meet your performance or data analysis needs.
*EtherNet/IP™ is a registered trademark of ODVA, Inc.
What is Quik-Cal™ and how do I use it?
One of the labor-saving features of DFE’s tension amplifier, indicator and controller products is Quik-Cal™ technology. It’s a feature integrated into almost all of DFE’s electronic products. With Quik-Cal™ the indication and control electronics use front-panel push buttons instead of potentiometers for zero and calibration settings.
• No tension display is needed
• No screwdriver is needed
• No second person is needed for setup or calibration
• Each button is pressed once during the calibration procedure for one second and the settings are stored automatically
Most of DFE’s tension indication and control products use Quik-Cal™ including the TrueTension™ TA1, TI17C, TI18C and TI22 amplifiers.
ZERO Set
Because an output signal is generated by the weight of the bare transducer roll in the system, we can negate the roll weight output component in a procedure called ‘zeroing’. To set the indicator output to ZERO when there is no tension, the ZERO button is pressed for one second.
With Quik-Cal™ the zeroing step can even be eliminated altogether, if desired. The tension indicator can be adjusted so that it automatically sets the output to ZERO when power is turned on. This is achieved by changing a jumper setting on the circuit board.
CAL Set
Once the indicator is zeroed, calibration is completed by hanging a known weight on a cord between the idler rolls in the machine web path such that the wrap angle over the transducer roll is kept identical to the one used in operation.
When the CAL button on the front of the indicator is pushed and held for one second, the calibration setting is stored. The indicator automatically multiplies the calibration weight by the preset calibration ratio to calculate the full-scale output of the indicator, and the indicator is calibrated and ready for operation.
What’s Calibration Ratio?
The calibration ratio is a multiplier value that the indicator uses to calculate the tension required to generate the indicator’s full output. It can be one of two preset values. The user can choose either 10%, which is the default value, or 25%, which may be preferred for lower tension measurement. The calibration weights chosen by the user will represent either 10% or 25% of the maximum tension the machine is expected to be running.
The standard calibration ratio is 10% (1:10). So, if a 10 lb weight is hung for calibration, and the CAL button is pushed, the indicator will store that value as 10% of its full output. Then 100 pounds of tension on the transducer roll (10 x 10) during operation will result in the indicator producing its full-scale output.
If the calibration ratio of 25% is selected instead, a 25 lb calibration weight (25 x 4) would also represent 100 lbs of output at full-scale, after calibration.
To switch between the 10% and 25% calibration ratios on the TI17C, TI18C or TI22 a jumper is moved on the circuit board. On the TA1 amplifier, the technician simply holds the CAL button for 2 seconds for 10% calibration or 8 seconds for 25% calibration.
Stability
Another benefit of Quik-Cal™ technology is inherent stability. The ZERO and CALIBRATION settings are stored digitally, so there is no drift over time and temperature variations as there can be with potentiometers.
Can DFE transducers be used in a vacuum environment?
Yes! When specifying transducers for use in a vacuum application, DFE will ask for additional application information. We’ll need to know what model tension transducers are desired, the level of vacuum under which the transducers will operate, and the specific process that they’ll be used for.
Because of out gassing and air entrapment within a transducer under vacuum, we can’t simply install a standard transducer into a vacuum chamber. Each of the fasteners used in the transducers must be modified to allow evacuation of the air within the cavity. Any lubricants used in the transducer bearings must be prescribed for use in a vacuum. All connectors and cabling must be compatible with vacuum use, and the standard RTV coating that DFE uses on the transducers must be left out of the process.
We must also know what temperatures the transducers will be exposed to in the chamber. In some cases the transducers may need to be moved to another roller due to a temperature extreme present at the intended roll position in the machine web-path. Please ask a Dover Flexo Electronics Applications Engineer for assistance in specifying a particular tension transducer for use in a vacuum application.
PRODUCT SPECIFIC QUESTIONS & ANSWERS
My tension amplifier (or indicator) will not calibrate, what am I doing wrong?
DFE amplifiers with Quik-CalTM may be unable to calibrate under certain error conditions, such as –
Minimum calibration offset has not been reached (cal weight too light)
Wire connections are incorrect
Bad cable continuity
Load cell excitation failure
DAC/ADC failure
Second generation Quik-CalTM amplifiers and indicators such as the TA1, TA500 and TrueView 1100 provide visual feedback to help identify error conditions and simplify the troubleshooting process.
Consult the relevant product manual to identify error codes and determine corrective action.
What is Extended Range (XR) option and why would I use it?
Extended Range output, or XR as abbreviated, is the name of an option that we offer with tension transducers (load cells) and corresponding amplifiers/indicators. By doubling the excitation voltage to a given transducer from 5 VDC to 10 VDC, the transducer produces twice the signal output. With some legacy amplifiers and indicators this improved the signal output quality at the low end of the transducer’s operating range. Transducers with the XR option must be used in conjunction with amplifiers with the XRE option such as the TI17C, TI18C and TI22 to experience any performance benefit. Note: Amplifiers configured for XRE (10 VDC) output should not be used with standard 5 VDC load cells, as this will shorten service life.
As signal processing techniques have improved in recent years, our newest electronics – used in conjunction with standard excitation transducers, have been shown to deliver the same performance as legacy XR systems. DFE’s newest TA1 TrueTension™ amplifier and TrueView™ 1100 series tension indicators are capable of delivering the same calibration scale and stability with 5 VDC transducers.
Your newest amplifiers and indicators no longer have a jumper for 10V Extended Range (XR) load cells, are they still compatible?
The latest generation of tension amplifiers and indicators such as the TA1, TA500 and TrueView 1100 are 100% backward compatible with standard (5V) and extended range (10V) load cells. Our engineers have fine-tuned amplifier excitation voltage to a level that maximizes load cell longevity while minimizing thermal drift. In addition, more advanced processors and signal processing techniques provide sensitivity that meets or surpasses earlier voltage-boost methods.
How do I tell if Taper Tension is needed on my rewind?
As a rule of thumb, any roll build in excess of about 20″ will require taper. If you are experiencing crushed cores, telescoping or stared rolls, or deformed material at the center of rolls, taper is also required. In most cases paper rewinds will require taper.
How do DFE Silencer™ pads work?
The Silencer™ pad’s patented design incorporates a laminated vibration absorbing layer which has been shown to be over 99% effective at eliminating brake squeal.
The digital meter on my SteadyWeb™ tension controller fluctates rapidly through a wide range, what is happening? Can I adjust to correct the problem?
Question: I have a SteadyWeb™ tension controller with a digital meter. The meter reads out a steady 133 pounds when tension is applied and the web is stopped, but when running web it fluctuates rapidly through a wide range, e.g. 95-133, with the result that I don’t see a useful tension reading. Is my running tension really changing that much that fast? Should I adjust the SteadyWeb™?
Answer: It is difficult to be sure what the digital tension meter is reading if it shows rapid fluctuation. This phenomenon may indeed be caused by variation in your running tension. To identify whether or not the problem is from instability in your running tension, connect an analog volt meter (10 VDC scale) between connection points 42(-) and 44(+) on the terminal block TB204 of the SteadyWeb™ power board. On the volt meter you can observe the actual signal variation rather than the amplified “flicker” seen on the digital meter.
It should be possible to adjust the meter damping to help reduce the flicker. This is a process of “averaging” the tension signal over a longer time period. Regardless, even a stable tension reading on a digital meter is not truly representative of the actual tension signal at any given point in time. Very slight web tension changes cause continuous signal variation.
In manual mode my SteadyWeb 12P can have tension set to 145 lbs. When I switch to Auto mode and turn the tension knob fully clockwise I can only get up to 100 lbs. What is wrong?
This problem is usually the result of the automatic tension setting being limited by an internal setting, and thus not allowed to output it’s full signal. One likely cause is the tension trim potentiometer being set at less than 100%. On the SteadyWeb Control Board check that the Tension Trim Pot (RT105) is turned fully clockwise. If so, check the + LIMIT pot (RT106). It should be turned fully clockwise as well.
As an additional check, connect a volt meter between points 13(+) and 15(-) on terminal block TB203 of the SteadyWeb™ power board. At full output both Auto and Manual modes should be at 10 VDC.
How do I set (and read) the DIP switches on older DFE tension controllers (analog)?
Switch blocks all work the same: There are numbers running down one side and there is a line with the word “OPEN” on the other side. If a switch is pushed in on the numbered side, this means that switch is closed. If pushed in on the side reading “OPEN”, the switch is open.
The switch should be actuated by something with a point, such as a ball point pen, for proper closure (or change of setting) of the switch.
Do you need answers to questions not listed above?
Complete the form below and a DFE Applications Engineer will contact you shortly.
DFE does not share information with 3rd party advertisers.